Edge Profiles / Bevel Geometry
Primary industrial cutting methods:
- Crush Cutting consists of a rotating disc pressed into an opposing anvil, creating a crushing nip into which the material being cut is directed. The resultant nip force exceeds the ultimate yield of the material, and the material is severed along the nip line. It is a cutting method broadly used across industrial converting applications. (Converting Magazine Technical Forum, Nov. 1999)
- Burst Cutting consists of a driven knife with a razor-sharp edge piercing through the entire thickness of material being cut without the assistance of an opposing knife.
- Shear Cutting is the vertical displacement of the material as it enters a shearing nip between two opposing edges. The opposing edges can be two straight blades, as in a guillotine, or two rotating discs, as in a web-slitting machine. (Converting Magazine Technical Forum, Sep. 1999)
Edge profiles, applications and resultant cut dynamics:
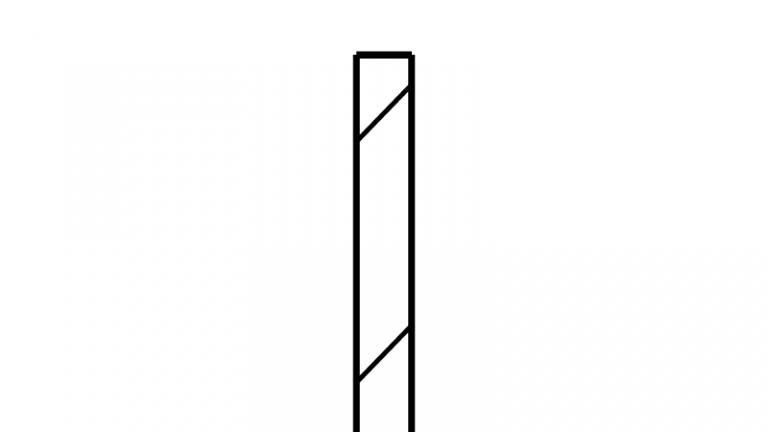
Square Edge
Used in heavy duty shear cutting against an anvil or similar square edge opposing edge
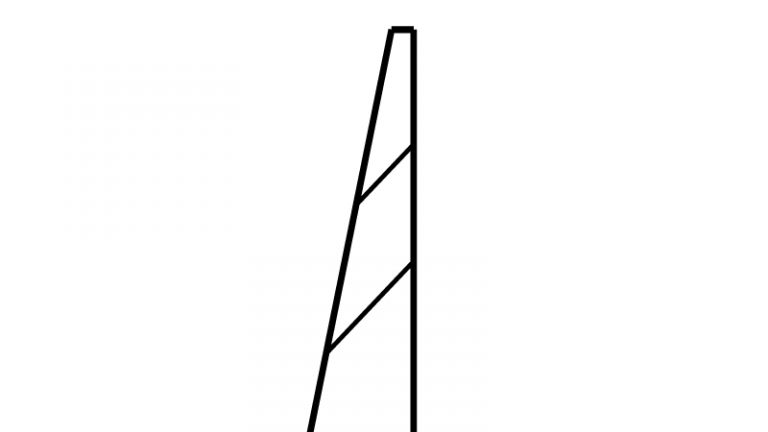
Single Bevel Blunt
Directional force applied on the blade perpendicular to an anvil. Used for parting material off, reducing pressure against the remaining monolith of material feed and promoting directional control of cut
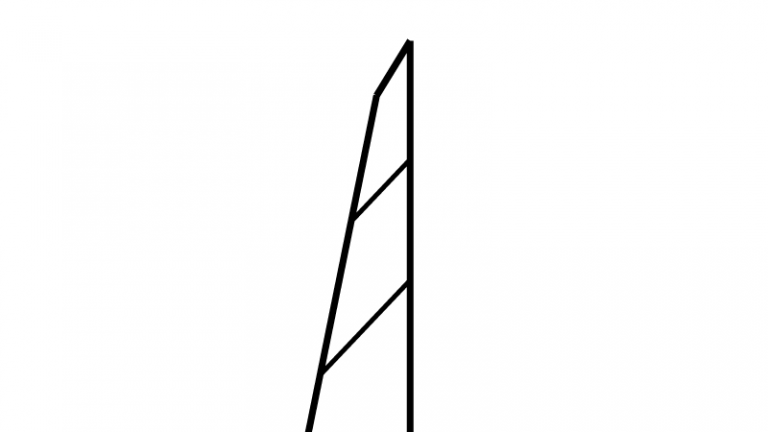
Single Bevel Sharp
Directional force applied on the blade perpendicular to a soft-core backing. Used for parting material off, reducing pressure against remaining monolith of material feed and promoting directional control of cut
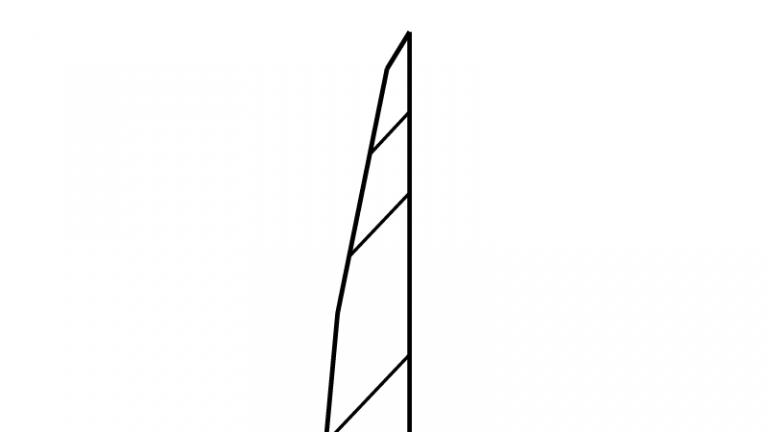
Compound Single Bevel
Directional force applied on the blade perpendicular to a soft-core backing. Used for parting material off, reducing pressure against remaining monolith of material and promoting directional control of cut with bevel geometry relieving pressure intensity on material being cut
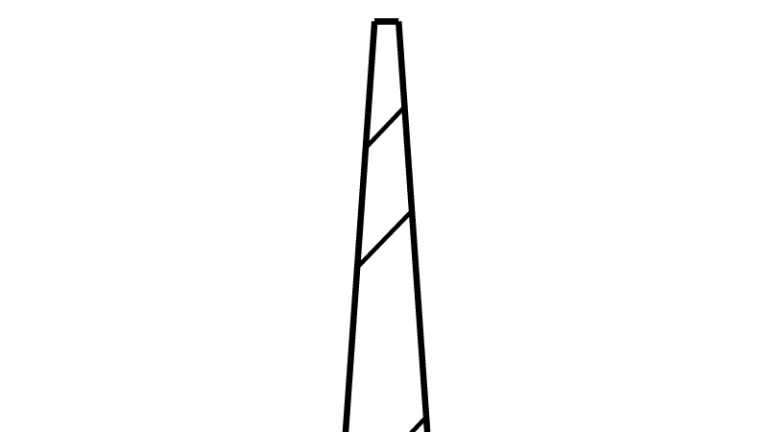
Double Bevel Blunt
Used in a crush cutting or “separating” application. Most commonly run in a set of knives attached to a single arbor or a “bank of knives” with directional force applied on the arbor perpendicular to an anvil
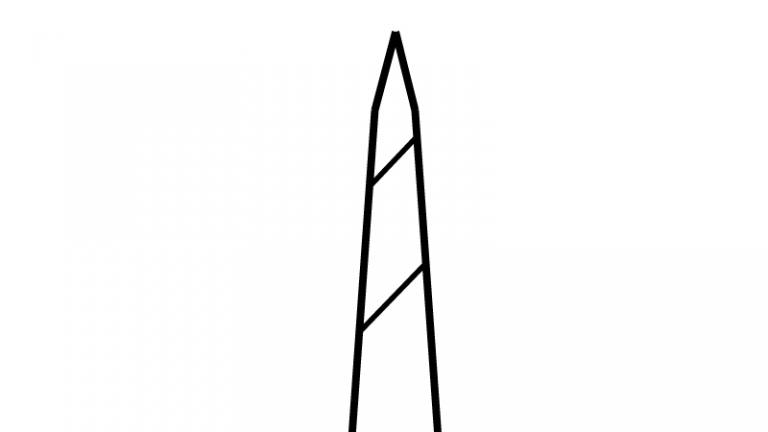
Double Bevel Sharp
Deep piercing capability which provides clean, straight cut lines due to initial razor-sharp penetration and balance of directional forces. The bevel geometry and length promotes separation of material
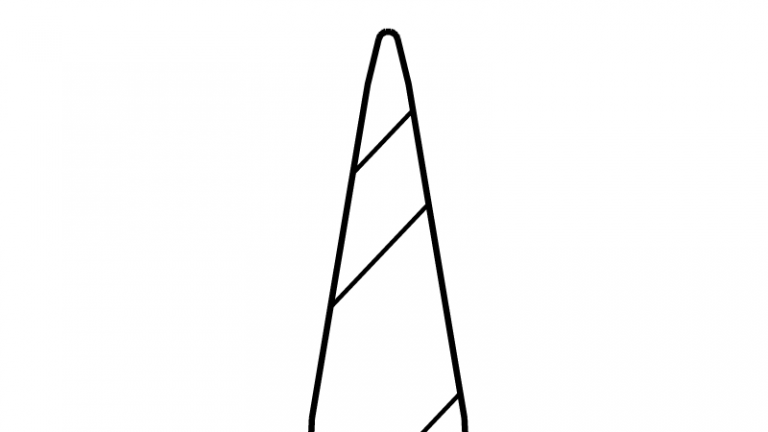
Compound Double Bevel
Deep piercing capability which provides clean, straight cut lines due to initial razor-sharp penetration and balance of directional forces. The bevel geometry and length promotes separation of material while simultaneously relieving pressure intensity on material being cut
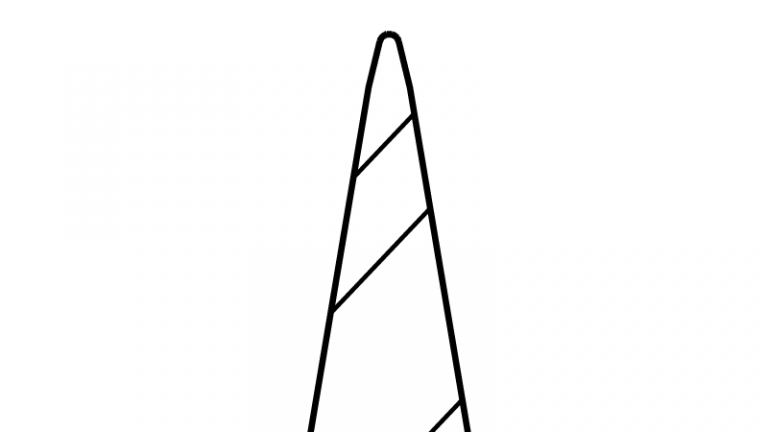
Double Bevel Radiused
Use in a crush cutting application, most commonly run in a set of knives attached to a single arbor or a “bank of knives” with directional force applied on the arbor perpendicular to an anvil
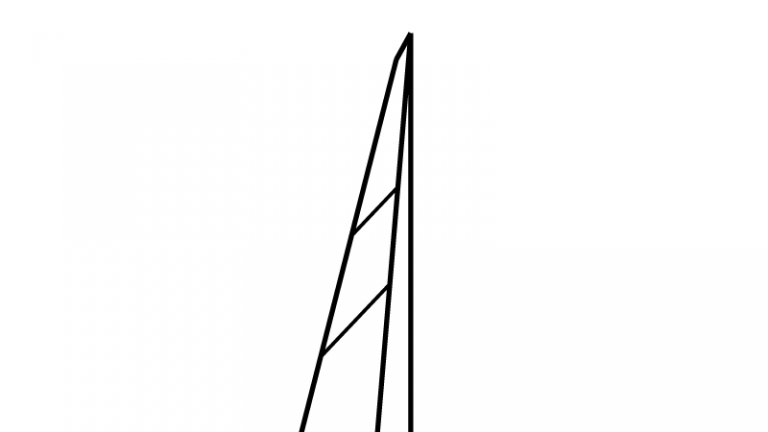
Reverse Bevel
Most commonly used in a shearing application, the reverse bevel allows the blade to clear the material after penetration
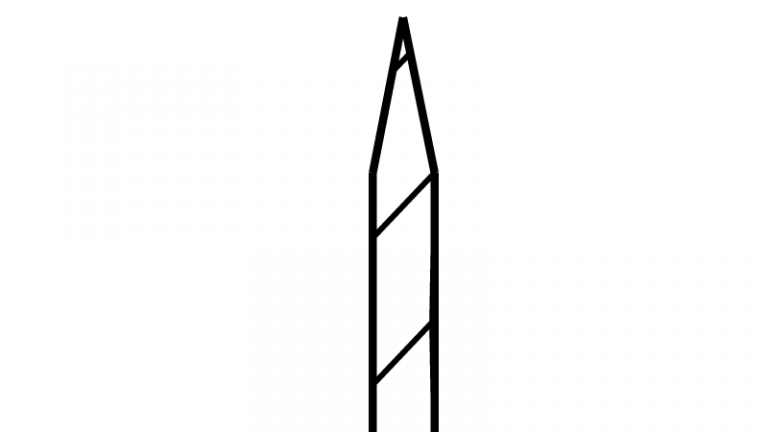
Hollow Bevel
Bevel geometry allows the blade to “spring” against the cut as the hub thickness intersects with the initial plunge depth
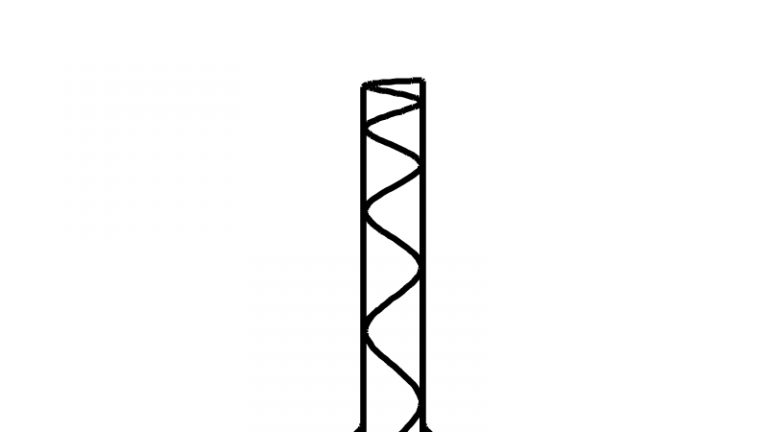
Scalloped Pattern
In a traditional converting application, provides increased linear cutting surface and rotation of cutting angles as material moves across each scallop. The resultant cut pattern reinforces edge strength of material and enhances anti-fraying quality
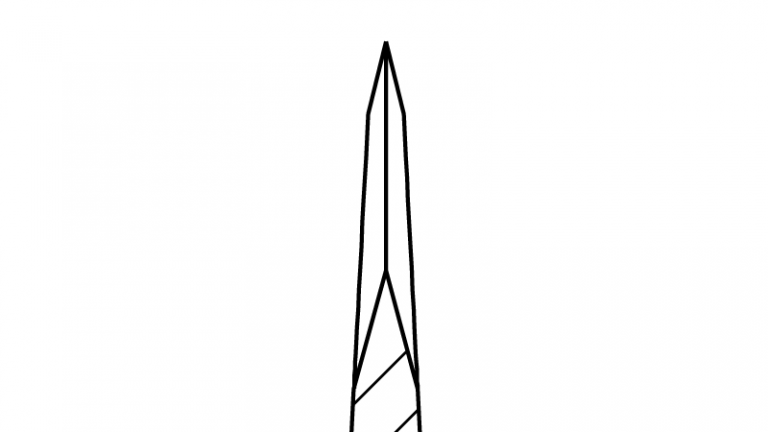
Scalloped / Serrated Pattern
In a rotational sawing or shearing application, provides increased linear cutting surface and rotation of cutting angles as material moves across each scallop / serration
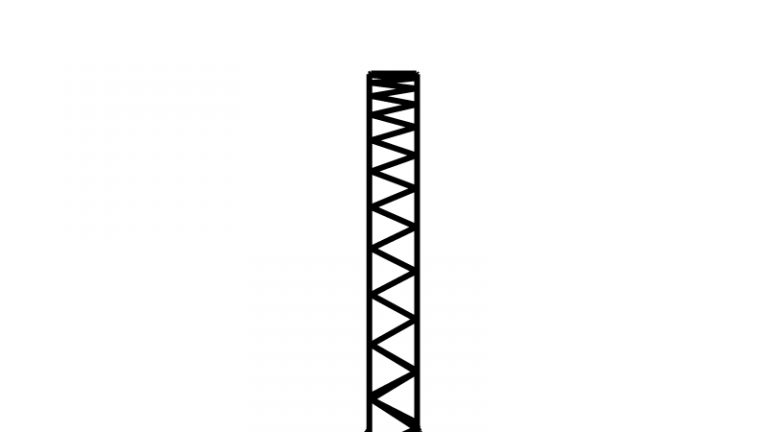
Pinker Pattern
In a traditional converting application, provides increased linear cutting surface and rotation of cutting angles as material moves across each scallop / resultant cut pattern reinforces edge strength of material and enhances anti-fraying quality